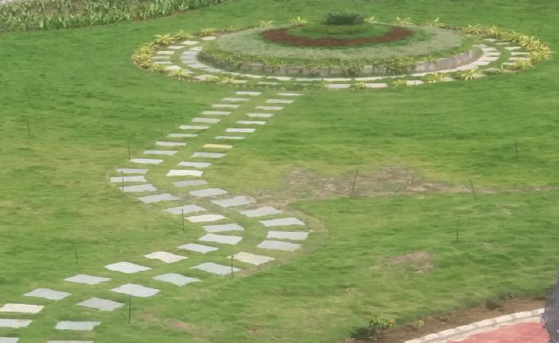
Resource Sustainability
Our vision of sustainability begins with manufacturing products using bio renewable raw materials and then ensuring that the full value of our raw materials is maximized. We begin by planning efficient manufacturing processes that enable economic sustainability for the company through higher product yields and environmental sustainability through use of fewer resources and low emissions and waste. We process every co-product as a feedstock for another value added product throughout the value chain.
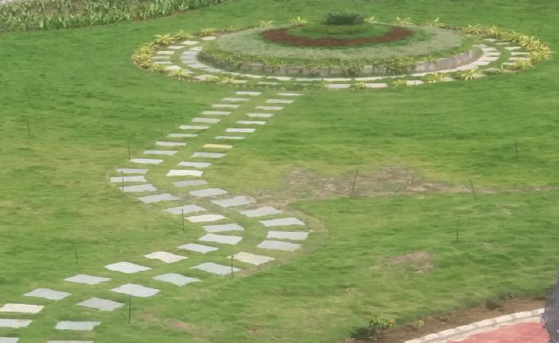
Envirnomental Clearance Certificate
M/s. Godavari Biorefineries Limited, A/P-Sakarwadi, Tal-Kopergaon, Dist-Ahmednagar – 413708 has been accorded Environmental Clearance, Vide No IA-J-11011/154/2019-IA-II(I) Dated 06.08.2021 from Ministry of Environment, Forest and Climate Change for Expansion of existing industry and addition of New Products of capacity from 6715 MT/M to 20090.94 MT/MEnvironment Clearance Certificate
EC Conditions compliance letter with Annexures Aug-Dec 2021
EC conditions compliance letter with Annexures Jan-Jun 2022
EC Compliance Report July 2022 to December 2022
EC Compliance Report October 2022 to March 2023
EC Compliance Report April 2023 to September 2023
EC Compliance Report October 2023 to March 2024
Recovering Value from Waste
Our approach to sustainability is to view the various effluents in the process not as a waste, but as a resource stream, and as a part of the manufacturing process rather than an ‘end-of-the-pipe’.
Our manufacturing plants established in 1939 have been transformed through several phases of development and investment.
Earlier, we only produced sugar, and molasses was a waste stream. Our company pioneered the use of molasses as a feedstock for making ethanol, and ethanol based chemicals. The spent from the fermentation process was then considered a resource to generate biogas, and then used the waste of this stream as an input feed to mix with the press mud to produce a compost called Bhumlabh.
Later, we pioneered the use of bagasse (also considered a fire hazard) as a feedstock for power generation and greenhouse gas mitigation. In fact, we were awarded a USAID grant for the same.
Our plants located in the states of Karnataka and Maharashtra use renewable resources to manufacture more than twenty products through the value chain from sugar cane to sugar, value added products like power, ethanol, bio-fertilizers and specialty chemicals.
Our integrated distillery system is designed for minimum steam consumption while producing rectified spirit and ENA directly from the fermented wash. Weak wash recycling reduces the quantity of effluent spent wash and also reduces the process water requirement of the plant.
Our Zero Liquid Discharge system involves a range of advanced wastewater treatment technologies to recycle, recover and re-use the treated wastewater thereby, ensuring no discharge of wastewater to the environment. The process condensate and spentleese are treated in a Biological Treatment Plant (BTP) and a condensing polishing unit (CPU). The treated water is re-used for process as well as cooling water thereby, reducing fresh water consumption.
As per the guidelines provided by the Central Pollution Control Board, CREP conditions, we have achieved 100% utilization of spent wash implementing a two-pronged approach. The spent wash generated in Distillery is burnt in an incinerator boiler helps in meeting the steam and power requirements of the distillery. Additionally, the ash from the boiler is used to make bricks further benefiting to reduce the environmental pollution and disposal problem & more importantly reduces the cost of construction. The rest of the Spent wash is used in the manufacturing of bio compost by utilizing press-mud received from our sugar mill, thereby leading to zero liquid discharge.
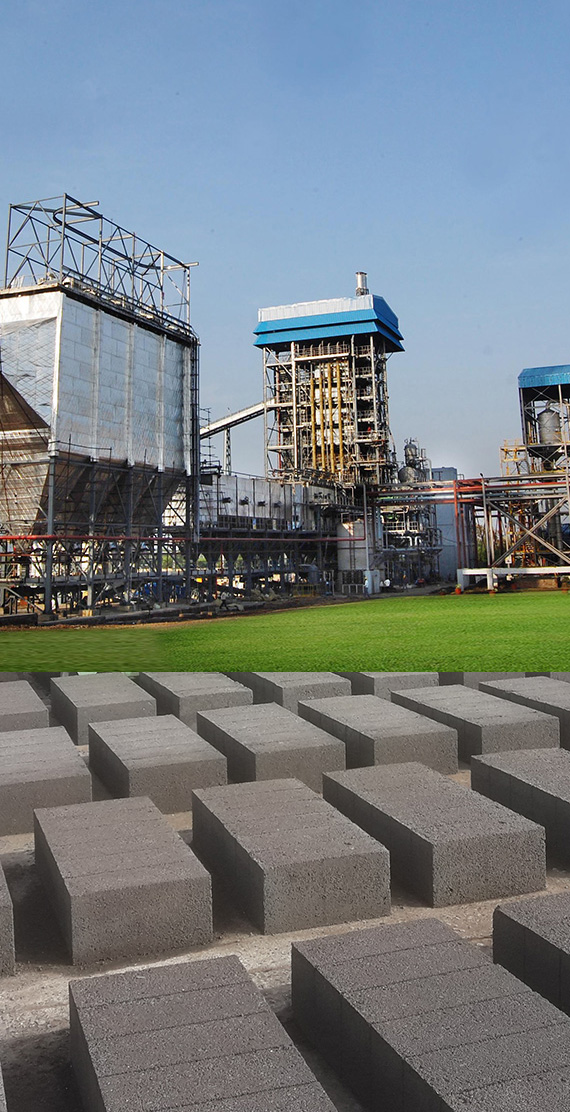
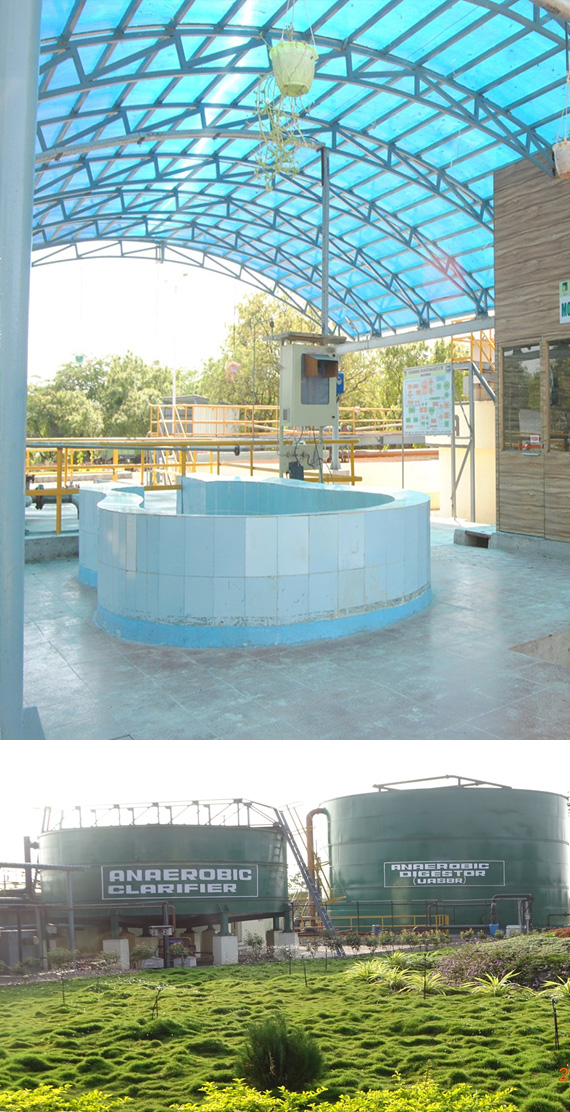
Water Sustainability
We recognise that water is a precious resource and are conscious of how we use it. Our several initiatives to reduce water usage include water treatment and recycling in all our plants enabling its reuse.
The sugar cane crop is about 70% water. This water is recognised as a resource, and is used in our processes to minimise the use of fresh water from the river. In total, over 400 cm3 of water per ton of cane crushed that currently comes from sugarcane is used in our operations.
Our integrated distillery system is designed for minimum steam consumption while producing rectified spirit and ENA directly from the fermented wash. Weak wash recycling reduces the quantity of effluent spent wash and also reduces the process water requirement of the plant.
Our processes involve a range of advanced wastewater treatment technologies to recycle, recover and re-use the treated wastewater thereby ensuring no discharge of wastewater to the environment. The process condensate and spentleese are treated in a Biological Treatment Plant (BTP) and a Condensing Polishing Unit (CPU). The treated water is re-used for process as well as cooling water thereby reducing the fresh water consumption.
We recognise the real use of water in the growing of sugarcane. And true water economy will only be achieved if we also examine water consumption in the fields. Some of these activities include trash mulching, alternate furrow irrigation, skip row irrigation, subsurface drip irrigation and frequent inter cultivation. Transplantation of sugarcane seedlings saves 30-45 days of irrigation compared to conventional sugarcane planting. Spraying Kaoline, which is a silica rich material, reduces trans evaporation loses from the plant. We have seen that drip irrigation saves around 40% water as compared to flood irrigation.
Energy Conservation
We believe in doing what is right and saving energy for a better tomorrow
TThe use of bagasse to manufacture surplus power in sugar mills only happened after the Government of India announced a policy to buy power generated by independent power producers.
Earlier, we used to generate power sufficient only for our own purposes. Now, with the same feed, we export more than 100 million units of surplus power to the grid, providing much needed power to the community and villages nearby. This process actually mitigates carbon emissions, and we actually earned Carbon Credits under the UNFCC
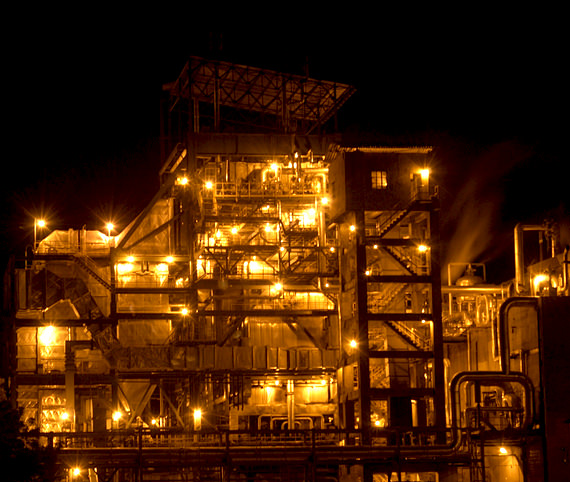
Healthier Earth
The earth has to prosper, and live. This can only happen if the practices we employ are sustainable, and our footprint is 'light'. Our resources come from the land, and we have to ensure that the soil, the earth is healthy. Too often, farmers use fertilizers on the basis of standard recommendations, without knowing what the farm actually needs. Our approach is to test the soil, understand what the farmer wants to plant, and then provide a range of options to the farmer, so that he or she can provide inputs to the soil, which will maximise his output, and leave the soil healthy for the coming years.
We further encourage the use of organic inputs, intercropping with soya etc, as further alternatives to ensure that the farmer meets the above mentioned objectives.